Cold gas coating – patented technology
for maximum induction performance
Patented cold gas spraying, e.g. for induction floors
Our innovative cold gas spraying process enables the precise application of coatings to rotationally symmetrical parts with a diameter of up to 400 mm. This state-of-the-art technology in the field of thermal spraying is primarily used in the manufacture of induction layers for aluminum and copper cookware.
Baf© - For the highest standards
- made in Thuringia
"Cold gas coating is like an
invisible bodyguard – it provides
precise protection, is extremely durable
and remains inconspicuously strong."
Awarded “Hidden Champion” status – patented technology for maximum induction performance
With its patented CSI process, BAF Industrie- und Oberflächentechnik GmbH is setting new standards in the refinement of induction pans. The Gigant Newline highlight series is the result of this innovative technology and impresses with its outstanding properties.
The benefits of our cold gas spraying:
- Up to 30% faster heating of cookware
- No flaking of the coating as with conventional thermal processes
- No risk of corrosion on the underside of the cookware
- The base remains uncoated and is polished to a shine
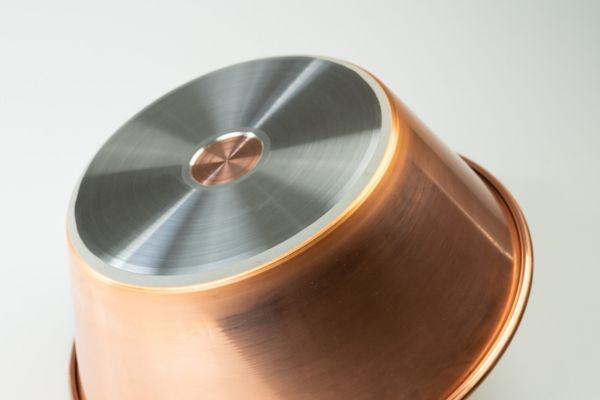
How does the cold gas process work?
In cold gas spraying, we use nitrogen as the process gas, which is fed through a spray gun at high pressure (up to 36 bar) and at temperatures of up to 720°C. The gas reaches supersonic speed and cools down significantly at the same time.
The coating powder is introduced into the gas stream and accelerated to speeds of up to 1200 m/s. Upon impact with the component, a solid, dense layer with optimum adhesion is formed.
We are your reliable partner
High-quality cold gas coating in Thuringia
Our patented cold gas spraying technology enables optimal heat transfer and durability in induction bases for aluminum and copper cookware.
Induction bases
The perfect choice for your aluminum and copper cookware. Thanks to our innovative cold gas spraying technology, we guarantee optimal heat transfer from the hob to your cookware.
Rotationally symmetrical parts
Our machine can process parts with a diameter of up to 400 mm; larger diameters require a customized solution.
Versatile applications
Also suitable for other coating requirements, e.g., the application of various precious metals such as gold or silver.
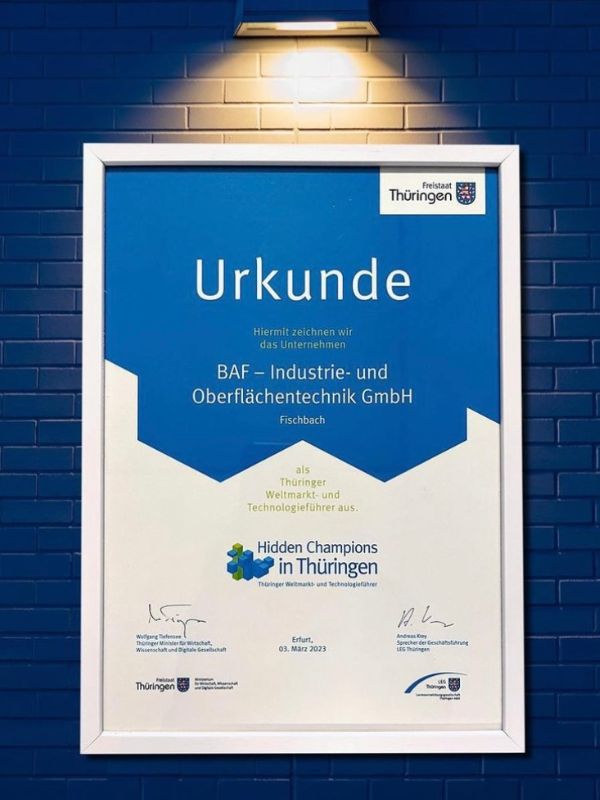
Do you have a project? We would be happy to support you.
Let's discuss your requirements – we offer free consultation, sampling, or a trial run.
FAQ Cold gas coating
What is cold gas coating?
Cold gas coating—also known as kinetic spraying—is an innovative process in which metallic particles are applied to the component at high speed. The advantage: an extremely adhesive, dense, and wear-resistant layer is created—without any thermal stress.
What are the advantages of cold gas coating?
Cold gas coatings effectively protect surfaces from abrasion, corrosion, and mechanical wear. They are ideal for components that have to function under extreme conditions—e.g., in aviation, mechanical engineering, or automotive technology.
For which materials is the process suitable?
Many metals such as aluminum, steel, copper, or titanium are suitable—mixed compounds are also possible. The process is particularly advantageous for heat-sensitive materials that are difficult to process with conventional coatings.
How thick is the coating in cold gas spraying
The layer thickness can be adjusted depending on the application and is usually between 50 and 500 micrometers. Higher layer thicknesses are possible on request.
What quantities are possible with cold gas coating?
We process individual parts as well as small and large series. Thanks to its fast and reproducible application, the process is ideal for industrial series production.